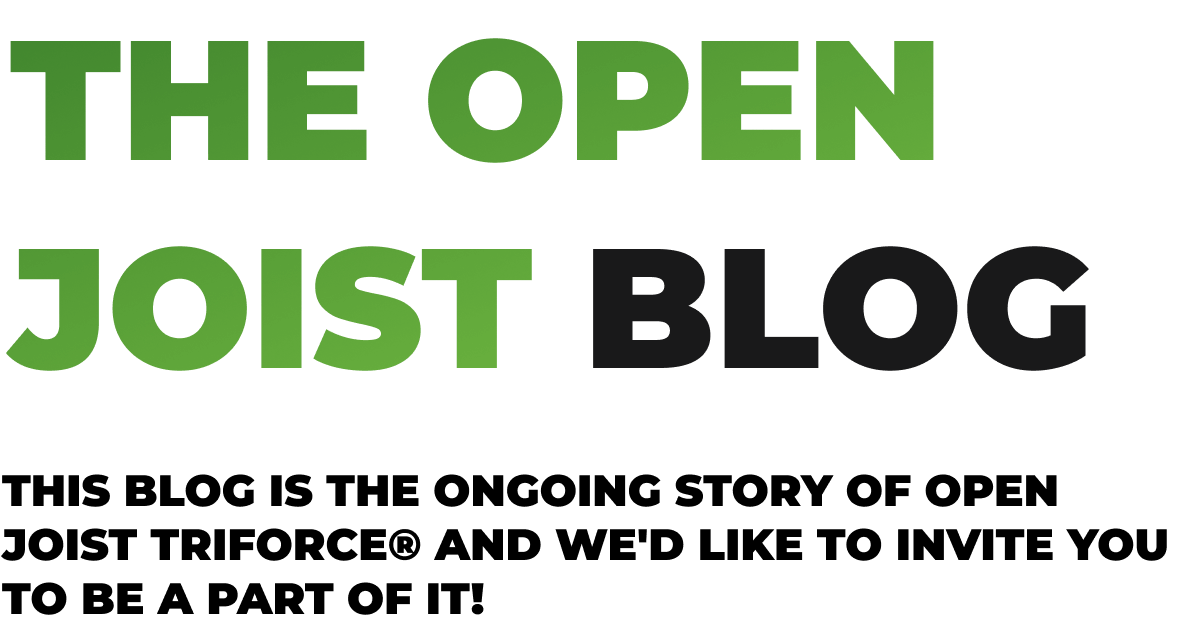
The TRIFORCE® blog is all about sharing our passion for building, either through our bloggers’ opinions on the market or on technical matters related to wood building. Through these articles, case studies and stories, we hope you’ll learn more about the open joist TRIFORCE® and floor system performance.
The TRIFORCE® blog is a forum for ideas and opinions and, by all means, we invite you to share your experiences in the response section. If the blog inspires you to seek actual technical advice suited to your circumstances, please don’t hesitate to reach out to us for a more in-depth conversation. We’ll be happy to help!
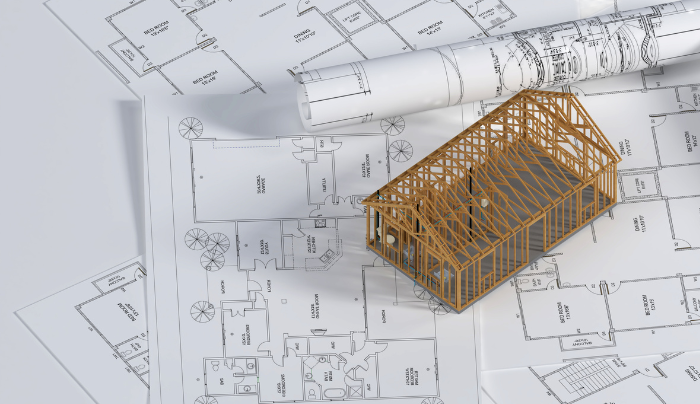
Let’s take a look at some TRIFORCE® projects with illustrations. See how to properly fasten your TRIFORCE® joists with hangers. We are going to examine some real-life cases of engineered wood floor joist structures. Take a closer look at the joists installation and other details that help you visualize how the floor is supported. These … Continued
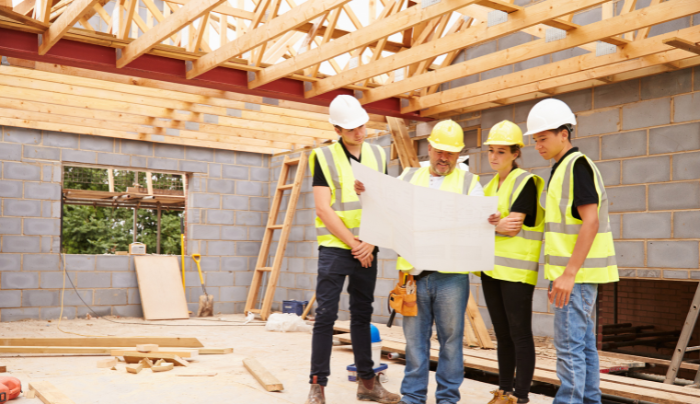
Thanks to its innovative design and eco-friendly materials, TRIFORCE® is revolutionizing the construction industry, find out how in this blog. Plus, learn how this open web joist speeds up work and improves a building’s structure and durability. If we pay attention to the issues facing the construction sector this year, we can quickly identify several: … Continued
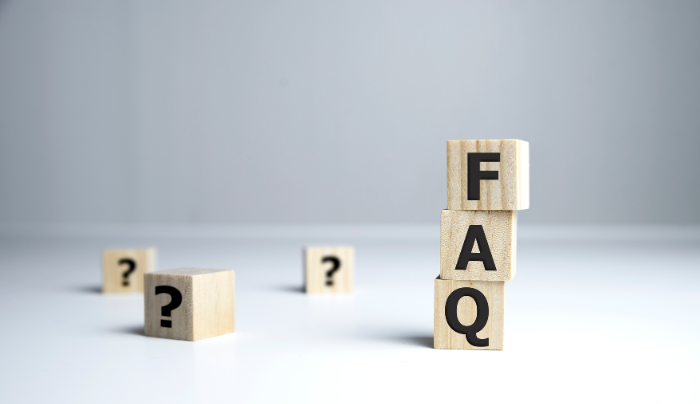
Thank you for taking the time to send us your requests and questions, it’s very valuable to us, and it is a pleasure to be able to answer or help you out. Throughout the year, the TRIFORCE® technical team does its utmost to respond quickly and appropriately to your immediate needs or questions. We have … Continued
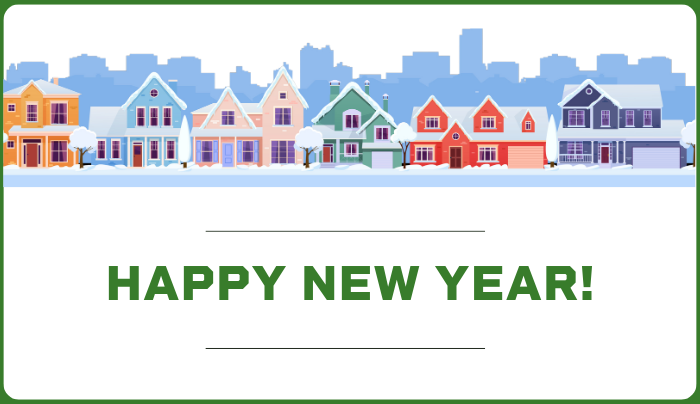
We can’t thank you enough for all of your support this year. From our entire team, we want to wish you a happy, healthy, and prosperous new year! Also, we want to share a sincere thank you for being a part of all of our monthly TRIFORCE® blog posts. We’re so excited to head into … Continued
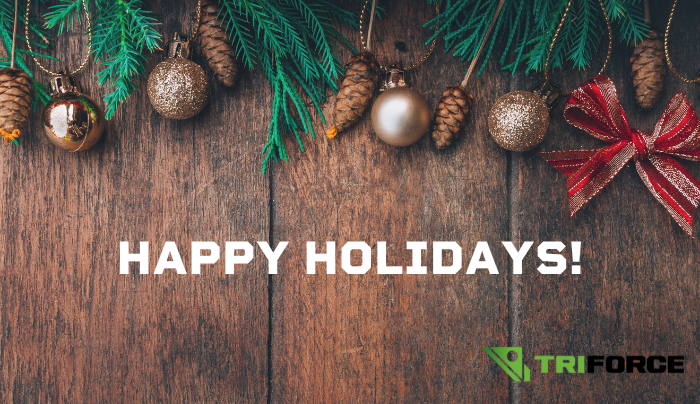
For some time now, truss shops have turned to TRIFORCE® open joist for their floor system because they realize the many benefits of these open web joists. These shops build their own plated floor trusses however, partnering with TRIFORCE® has allowed them to save time and money, resulting in additional sales. Some or all joist-dedicated … Continued
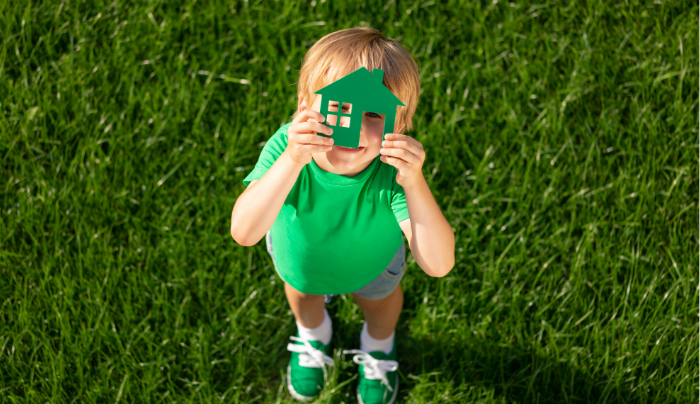
Open joist TRIFORCE® and plated trusses are both open-web but in fact, there are several differences. These two engineered wood floor joists have many characteristics that distinguish them from one another. Let’s review the positive impact of using TRIFORCE®, a finger-jointed joist, in lieu of plated floor trusses: Fire-resistance Ecologic Less expensive No delays No … Continued
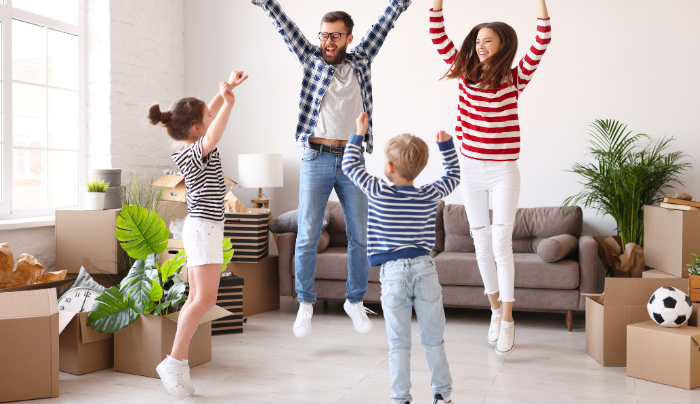
Most residential and commercial buildings are equipped with an air distribution system. It’s an important component of any HVAC (heating, ventilation, and air conditioning) system. Its primary function is to distribute conditioned air throughout a building or space, ensuring that the air is evenly distributed and that the temperature and humidity levels are consistent. Open … Continued
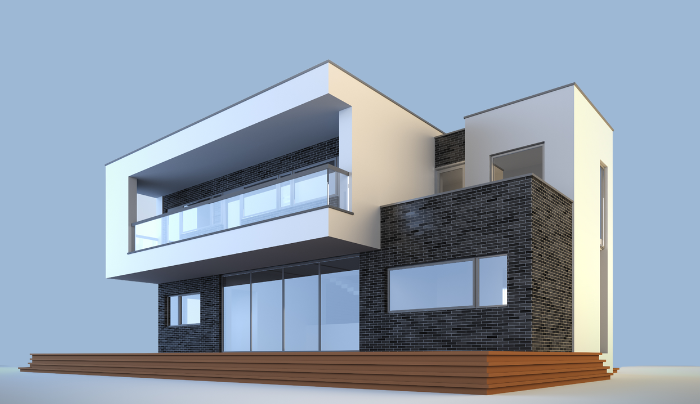
Have you ever heard of a cantilevered extension? If you work in the construction industry, you probably have an idea of what it refers to. Cantilevers are commonly used to extend the length of a floor system beyond the supporting wall or beam. It can be a simple balcony, or an entire room suspended on … Continued
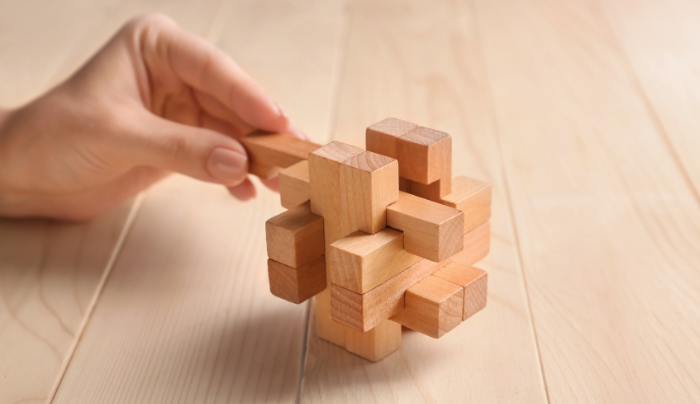
It may be common thinking to describe a floor only as a series of joists with secure floor sheathing on top of them. But, for it to be an effective floor system, there’s more to it than that. At TRIFORCE®, we aim to create floor systems that surpass industry standards, providing strength, durability, and comfort. … Continued
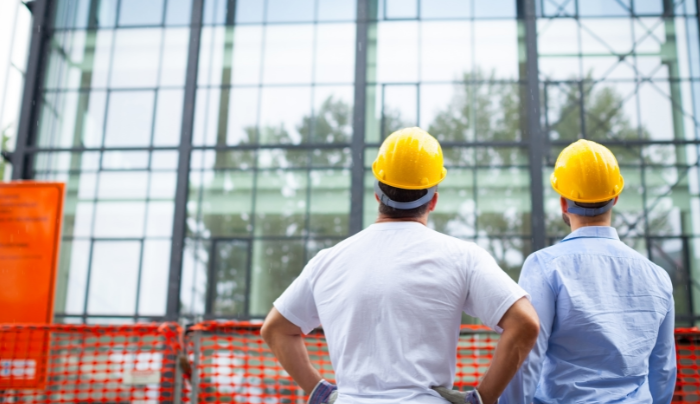
There are currently some challenges in the construction industry and we must be able to deal with them as quickly and efficiently as possible. This is why an open web floor system such as TRIFORCE® is a great solution to our problems. Here are present concerns that can be helped by using TRIFORCE® joists: 1) … Continued