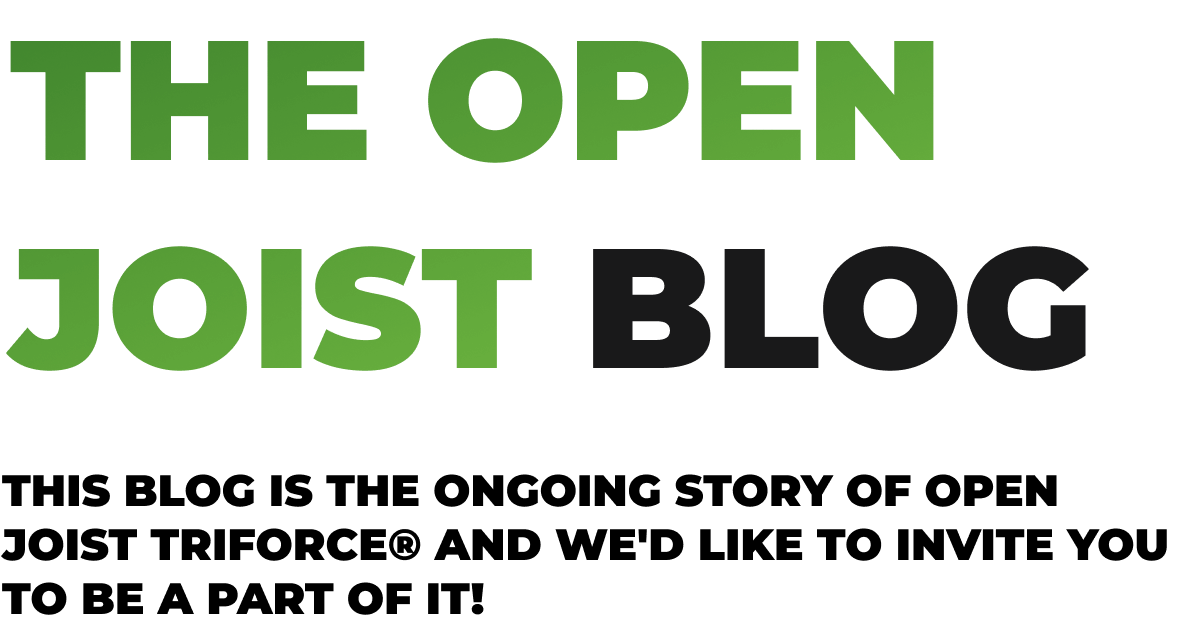
The TRIFORCE® blog is all about sharing our passion for building, either through our bloggers’ opinions on the market or on technical matters related to wood building. Through these articles, case studies and stories, we hope you’ll learn more about the open joist TRIFORCE® and floor system performance.
The TRIFORCE® blog is a forum for ideas and opinions and, by all means, we invite you to share your experiences in the response section. If the blog inspires you to seek actual technical advice suited to your circumstances, please don’t hesitate to reach out to us for a more in-depth conversation. We’ll be happy to help!
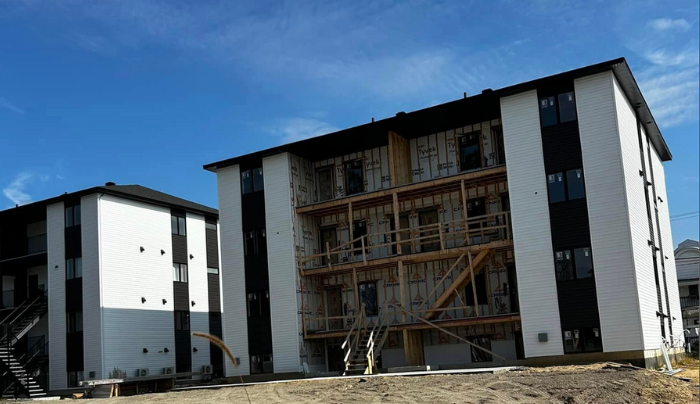
Discover a live construction project featuring TRIFORCE® open web joists, as shared by a local well-known and experienced Quebec contractor. Construction F. Therrien, generously took the time to share with us his experience with TRIFORCE® joists. Following this meeting, we’re delighted to share his comments with you and photos of the current construction site. A … Continued
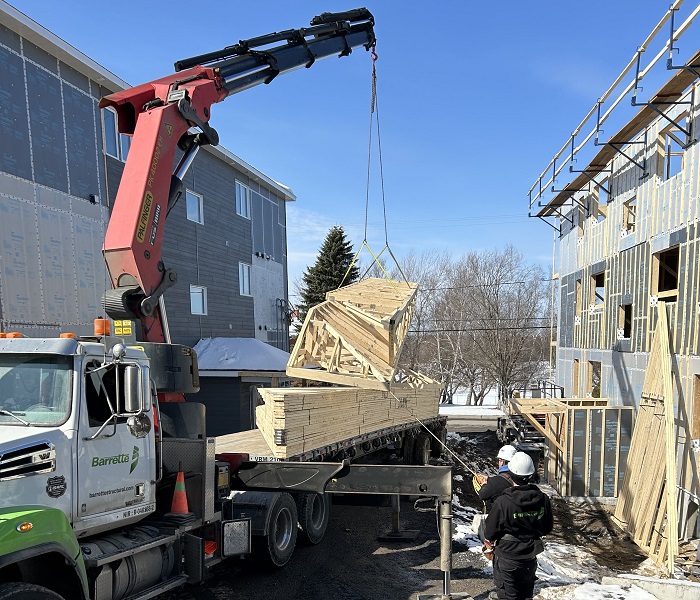
When it comes to designing high-performance, open-web structures, this question often comes up: Can TRIFORCE® joists be used for roof construction? The answer is yes—but only for non-sloped (flat) roof systems. TRIFORCE® open web joists offer several advantages in flat roof applications: Let’s take a look at each of them: Some factors to consider: However, … Continued
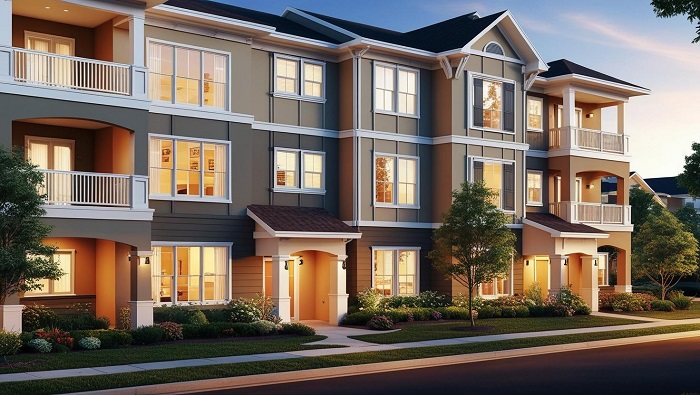
Discover how TRIFORCE® open web joists are revolutionizing multi-family construction, offering a faster, smarter, and more sustainable way to tackle the housing crisis. Why Canada and the U.S. are facing a housing shortage A growing challenge, impacting millions of people and driving up demand for efficient building solutions. Rising costs, regulatory delays, and limited housing … Continued
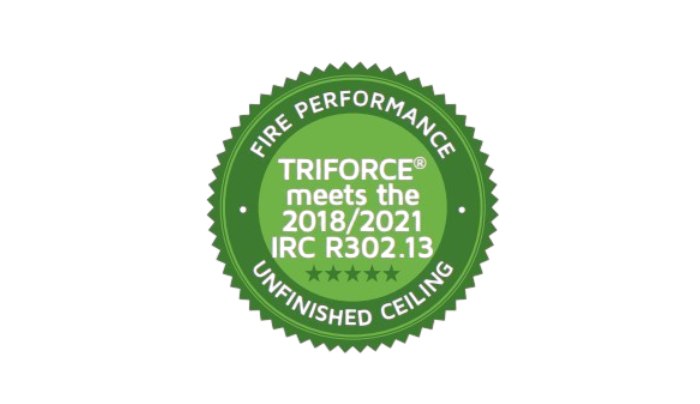
When it comes to innovative and safe construction solutions, TRIFORCE® Open Joists stands out as a leader in fire-resistant engineered floor systems. Designed to offer superior structural integrity and improved fire safety, these open web joists combine durability and flexibility for builders seeking reliable options. Fire is a major hazard in buildings, and it’s crucial … Continued
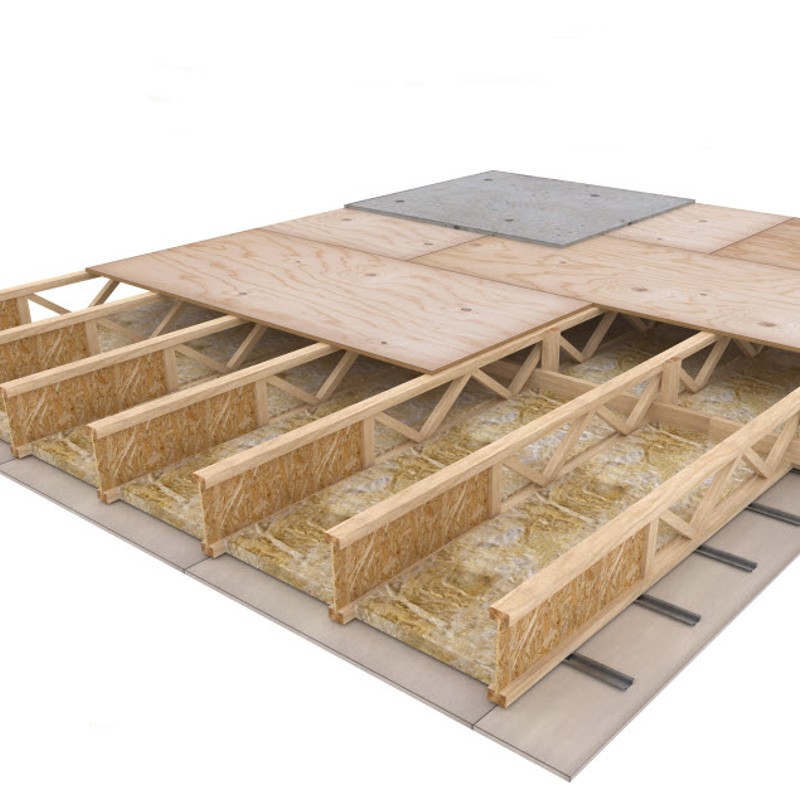
Guarantee the durability of your construction project with proper installation of TRIFORCE® open web joists and all other important floor components. Ensuring the correct installation of TRIFORCE® open web joists is critical to achieving a durable and efficient floor system. This blog will cover the key components of an open web floor structure and how … Continued
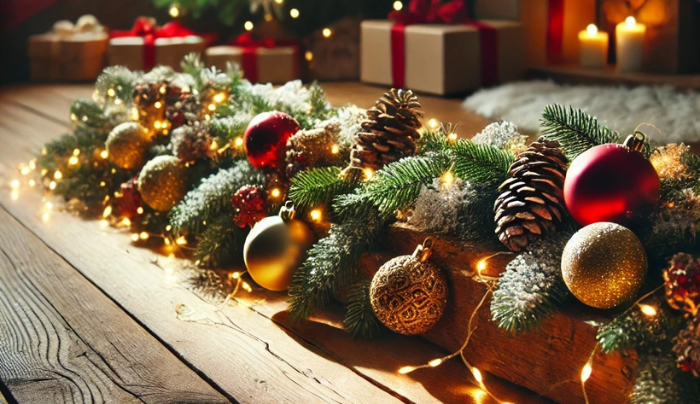
You are at the heart of everything we do, and we are grateful to you that we continue to progress and excel. As 2024 comes to a close, we want to sincerely thank you from the bottom of our heart for your trust and support throughout this year. We are thrilled to welcome the arrival … Continued
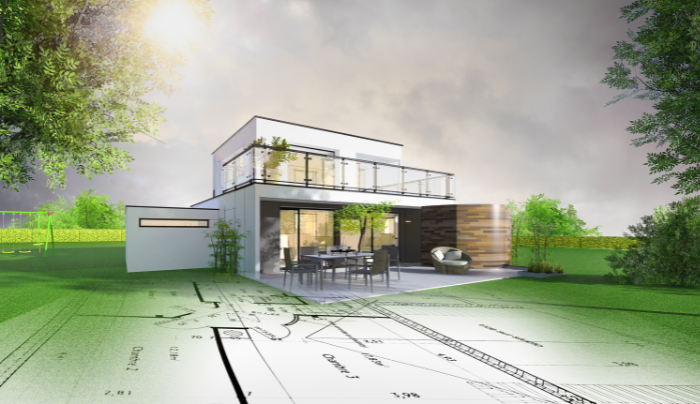
TRIFORCE® Open Joist introduces an innovative and user-friendly software for comprehensive engineering analysis, streamlining workflows from full-floor evaluations to accurate member sizing. TRIFORCE® Analyzer goes beyond standard software, it’s an indispensable asset for designing open web floor joist systems with precision. Tailored to meet the demands of engineers, architects, and contractors, it ensures projects prioritize … Continued
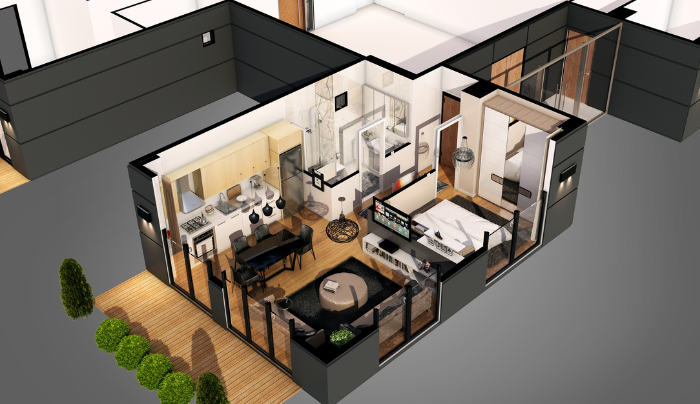
Discover how TRIFORCE®, its innovative design is a crucial element in modern construction, solving key challenges faced by today’s building professionals. On the market today, in the residential and even commercial sectors, we see buildings with particular structures that require materials that adapt to every possible case. In this blog, we take a look at … Continued
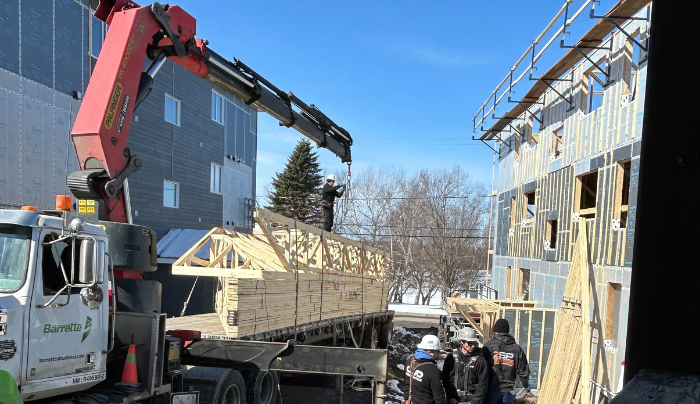
Discover an experienced contractor’s statement on using TRIFORCE® joists. He is very enthusiastic and highly recommends them based on his vast experience. To ensure the success of a construction project, it’s essential for builders to choose reliable, top-of-the-line materials that also offer good value for the money. This not only helps them meet their customers’ … Continued
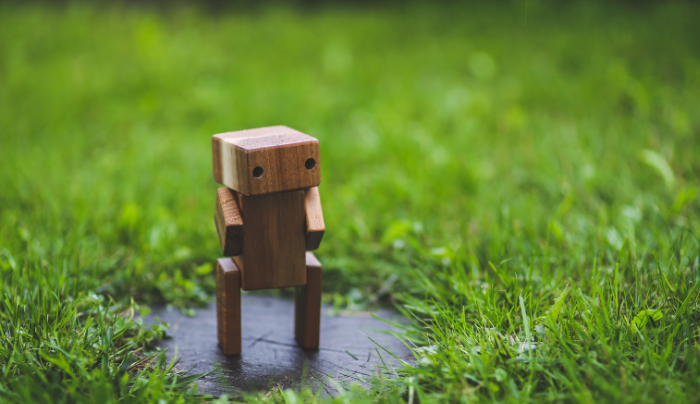
Find out why individually testing joists helps to ensure quality and customer satisfaction. It prevents many types of inconveniences and improves performance. This blog will explain why individually testing joists is crucial to ensure maximum quality. Not only does this process help to identify defects early but will improve product reliability and, by the same … Continued