We recently got a question on our website about how the joints are made on the open joist TRIFORCE®. It’s great question, as it touches on many of the product’s strengths.
We always welcome questions on our blog, so please feel free to ask. So, here’s our answer.
5-fingered-joints acting as connector
The first thing you’ll notice about the TRIFORCE® joist is that, although it has an open web design, there are no metal plates. The connection of its components relies on a simple yet effective technique that has been around forever: fingerjoining.
5 fingered joints connect the webbing to the chords. The chords themselves can have sections of wood that have fingered connections, depending on the desired length.
Although this technique has traditional origins, TRIFORCE® makes it quite sophisticated in its application. In each case, the fingered sections are inserted into the grooved ones along with Phenol-Resorcinol adhesive, under great pressure. We assemble the elements in a 100% robotic environment that’s highly precise.
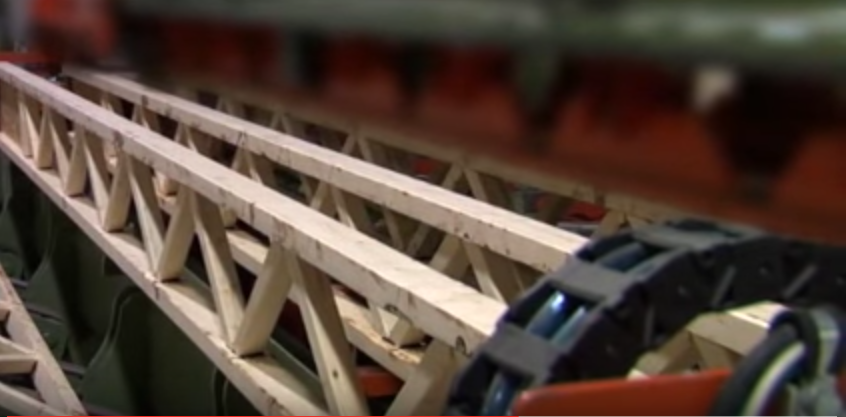
Strength of a triangular design
Stepping back a little, you’ll also notice the triangular design of the webbing. The open joist TRIFORCE® takes advantage of the natural strength of the Triangle to handle load.
So, in fact, TRIFORCE®’s strength comes from the combination of technology used for the finger-joint and the triangular design. The result is exceptional strength and stiffness. TRIFORCE® joists are individually tested for load capacity before leaving the factory.
A design that does away with metal plates has several advantages:
- No plate corrosion to deal with
- There is no potential damage to mechanical, electrical and plumbing equipment due to metal connectors, such as scoring of electrical wires
- No workers cutting themselves on the plates
- The all wood design and glued joints eliminate potential squeaking
- The open joist is light. Not only because of the absence of heavy metal plates, but also because there is no need for the webbing to be of the same size as the chords.
Light and easy to carry
The difference in weight is significant. It makes for a much lighter and more manoeuvrable joist. Given an equivalent length, one worker can safely carry two TRIFORCE® compared to the two workers it takes to carry the plated truss. This can lead to faster installation and cost savings. The initial cost for the TRIFORCE® is also considerably lower than a plated truss.
Finally, TRIFORCE®’s all-wood construction and fully automated fabrication process allows us to manufacture a product of highly controlled quality, reliability, and sustainability.
Our thanks to our reader for that question. Please don’t hesitate if you’d like to ask us anything about our product. We would be more than happy to reply.