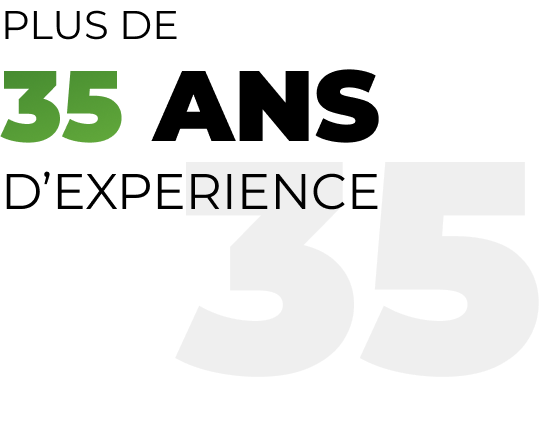
Une longue historique
TRIFORCE® offre plus de 35 ans d’expertise, s’appuyant sur la Open Joist 2000®, sa prédécesseure bien connue et développée à la fin des années ’80. Elle représente la synthèse des caractéristiques et avantages de tous les types de poutrelles combinés. Fabriquée dans une usine ultra-sophistiquée avec un procédé de fabrication 100% robotisé, la solive ajourée TRIFORCE® s’avère être un produit de très haute précision.
Sachant que la production de masse est essentielle pour la disponibilité continue des produits et que les installations de production de TRIFORCE® sont entièrement automatisées, l’usine peut accélérer la production rapidement pour répondre à la demande. L’usine est également conçue pour fonctionner 24/7 tout en offrant la plus haute qualité.
Une usine unique en son genre
L’un des plus grands bâtiments industriels en bois lamellé-collé de l’Est du Canada
En 2009, Barrette Structural Distribution, une division de Les Entreprises Barrette, un chef de file dans l’industrie depuis plus de 50 ans, a reconstruit une toute nouvelle usine pour fabriquer la solive ajourée TRIFORCE®. Cette installation est le plus grand bâtiment industriel fait de bois lamellé-collé de l’est du Canada et couvre plus de 180,000 pieds carrés. Barrette s’est non seulement assurée que son usine soit à la fine pointe de la technologie et qu’elle mise sur un assemblage robotisé précis et efficace de ses solives, elle a également misé sur la construction d’une usine durable et verte. Fait principalement de bois, ce bâtiment emmagasine 925 tonnes de GES, soit l’équivalent de la production annuelle de 185 Canadiens.
La poutre la plus impressionnante du bâtiment mesure 80 pieds (24,3 m) de long, 6 pieds 6 pouces (2 m) de haut et 14 pouces (356 mm) d’épaisseur. Sa teneur en bois pèse plus de 22 000 lb (10 000 kg).
Les quatre poutres principales mesurent 350 pieds (107 m) de long après assemblage, 4 pieds (1,2 m) de hauteur et 11 pouces (280 mm) d’épaisseur.
Au total, 1 119 pièces de bois ont été utilisées pour construire cette structure unique en son genre.
L’usine TRIFORCE®: une conception et un processus respectueux de l’environnement
Plus de 97% des matières premières utilisées dans la production
- Tous les matériaux résiduels générés par la production de la poutrelle ajourée TRIFORCE® sont entièrement récupérés et utilisés. Pour cela, nous avons installé un dépôt pour les résidus de bois qui seront ensuite transformés en sous-produits. Peu fréquent dans l’industrie, l’utilisation d’un tel dépôt est une avancée majeure dans la protection de l’environnement.
- Le programme d’optimisation des matières premières de Barrette Structural Distribution comprend également la récupération des poutrelles présentant de légères imperfections. Puisqu’elles ont une extrémité ajustable, il n’est plus nécessaire de les dévaluer comme de simples sous-produits. L’usine a donc considérablement réduit ses pertes de matières premières et affiche désormais un taux de perte aussi bas que 3%.
Des économies d’énergie massives pour réduire l’empreinte carbone
- L’usine de fabrication de Barrette Structural Distribution est alimentée à 100% par l’hydroélectricité, une énergie totalement propre. Pour minimiser davantage notre empreinte écologique, nous nous sommes assurés d’utiliser le moins d’énergie possible pour gérer nos opérations. Puisque le soleil nous fournit une énergie gratuite et constante, nous avons installé des murs solaires! Combinés à une isolation intelligemment conçue, ces murs nous ont permis de générer une partie substantielle de l’énergie nécessaire pour chauffer l’usine et, en retour, cela s’est traduit par des économies massives et une empreinte carbone largement réduite.
Développement durable
Le procédé de fabrication de TRIFORCE® est unique car son bois provient principalement de la partie inutilisée (la tête) d’épinettes noires des forêts matures du Québec. Ce procédé utilise quatre fois moins d’énergie que celui du béton et 60 fois moins que celui de l’acier. L’utilisation de la partie inutilisée de l’arbre entraîne une réduction des émissions de gaz à effet de serre (GES).
Voici quelques-uns des principes du développement durable que nous appliquons:
- Soutien à l’industrie canadienne du bois et à ses travailleurs
- Bois issu d’une forêt certifiée respectant les principes de la foresterie durable
- Utilisation de ressources locales et renouvelables
- Economies d’énergie: compte tenu de son faible facteur de transmission thermique, le bois est 12 fois plus isolant que le béton et 350 fois plus que l’acier.
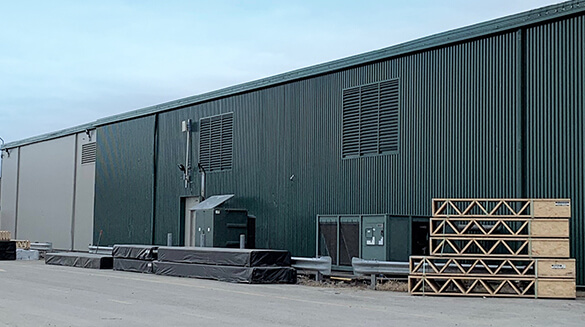
Prendre avantage sur des murs solaires
Les murs solaires de l’usine TRIFORCE® sont perforés de milliers de petits trous créant des turbulences et permettant à l’air chauffé par le soleil de passer à travers la paroi de couleur sombre. L’air ainsi chauffé est ensuite capté et mis en circulation par des ventilateurs. Les murs solaires sont orientés vers le sud-est et le sud-ouest et, comme ils sont de couleur vert foncé, ils absorbent plus de chaleur; ce qui augmente leur efficacité. En fonction de la saison et de l’ensoleillement, la température de l’air monte de plusieurs degrés, ce qui représente une économie d’énergie considérable!
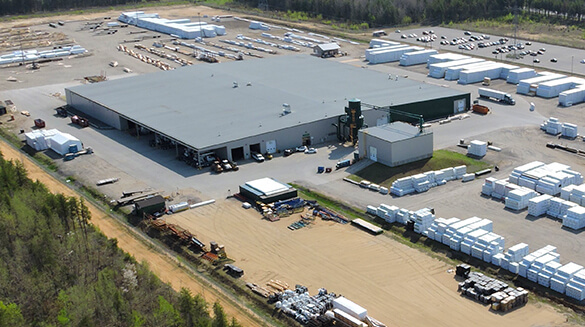
Isoler avec esthétisme
Les 440 panneaux préfabriqués qui constituent le mur extérieur ont une finition identique des 2 côtés et comportent une mousse isolante de type 1 ayant une valeur élevée (R21). Ces panneaux ont été installés sur toute la surface extérieure des murs jusqu’à 6 po (150 mm) du sol, de façon à recouvrir toute la partie visible du béton. Cette façon d’isoler améliore significativement la performance énergétique du bâtiment.
Cachez ce câblage!
Pour des raisons esthétiques, l’équipe de projet a décidé de camoufler la majorité du câblage électrique. C’est ainsi que 8 km de tuyauterie ont été installés sous le plancher pour, au total, contenir 25 km de câblage électrique.